What is Work in Progress?
Work in Progress (WIP) refers to incomplete goods still in the production process, i.e. the manufacturing stage between raw materials and finished goods.
- Work in progress (WIP) represents partially finished goods that are still undergoing production, positioned between raw materials and finished products in the manufacturing process
- The calculation of WIP inventory is determined using the formula: Ending WIP = Beginning WIP + Manufacturing Costs – Cost of Goods Manufactured (COGM)
- WIP inventory is classified as a current asset on the balance sheet, reflecting the efficiency of inventory turnover and its potential conversion into cash within a twelve-month period.
- Companies typically aim to minimize the duration that inventory remains in the WIP stage, as prolonged WIP periods can indicate inefficiencies and negatively impact free cash flow (FCF).
- Effective inventory management necessitates industry-specific benchmarks for WIP, emphasizing the importance of internal comparisons and avoiding cross-industry evaluations to accurately assess performance.
How to Calculate Work in Progress (WIP)
WIP stands for “work in progress” and refers to any partially complete inventory not yet ready to be sold to customers.
At the WIP stage, these inventory items are not marketable and require more time before it can be sold on the market.
The term work in progress (WIP) describes inventory that is partially finished and currently amid the production cycle.
For instance, the WIP inventory could be undergoing finishing touches prior to being marked as complete.
There are three stages that inventory – a current asset on the balance sheet – can be classified into:
- Raw Materials → The materials on hand that are part of the production process, e.g. commodities.
- Work In Progress (WIP) → The process of turning the raw materials into finished goods has begun, however, the item is not yet ready to be sold.
- Finished Goods → The production process is complete and these items are now ready to be sold.
Once the product is marked as a finished good and is subsequently sold, the appropriate amount is removed inventory balance on the balance sheet.
On the income statement, the sale of the product would be recorded in the cost of goods sold (COGS) line item.
Work in Progress Inventory Formula (WIP)
The formula for calculating work in progress inventory – in the specific context of a manufacturer – is as follows.
The beginning work in progress inventory is the ending balance from the prior accounting period, i.e. the closing carrying balance is carried forward as the beginning balance for the next period.
The manufacturing costs are then added to the beginning balance.
Manufacturing costs are a bit of an open-ended term but refer to any costs incurred related to the process of manufacturing raw materials into a finished product, e.g. the cost of raw materials, labor, and overhead costs.
In the final step, the cost of manufactured goods (COGM) is subtracted.
COGM is defined as the total costs incurred while creating a finished product, and in order to estimate the value of a company’s end-of-period WIP, the finished COGM is a necessary input.
COGM can be determined by adding the total manufacturing costs to the beginning WIP inventory, followed by subtracting the ending WIP inventory.
How to Analyze WIP Inventory in Accounting
Work in progress inventory can be found in the current assets section of the balance sheet, which reflects how inventory is expected to cycle out within a twelve-month period, i.e. be converted from raw materials into cash.
Generally, most companies strive to reduce the amount of time that inventory spends at the work in progress (WIP) stage.
- Longer WIP Stage → The longer the items remain in the work in progress stage, the less efficient that company may be – all else being equal.
- Shorter WIP Stage → The quicker the inventory cycles out (i.e. as part of the cash conversion cycle), the more free cash flow (FCF) there tends to be since the cash is not merely sitting as inventory.
However, different industries will have different targets for their inventory management KPIs, particularly for more technical, manufacturing-intensive products that require substantially more time to pass through the WIP stage.
Therefore, it is also essential to make internal comparisons (i.e. track the changes in WIP year-over-year), as well as avoid making comparisons between companies operating in entirely different industries, i.e. stick to the company’s closest competitors and other industry peers to determine the proper target WIP benchmark.
Work in Progress Calculator (WIP) — Excel Template
We’ll now move to a modeling exercise, which you can access by filling out the form below.
Work in Progress Inventory Calculation Example (WIP)
Suppose a manufacturer is attempting to calculate its work in progress (WIP) for the end of the latest fiscal year, 2021.
Q. If the beginning WIP balance is $20 million, the manufacturing costs were $250 million, and the cost of goods manufactured (COGM) is $245 million, what is the ending work in progress (WIP) balance?
The assumptions that our model will use are as follows.
- Beginning Work in Progress = $20 million
- Manufacturing Costs = $250 million
- Cost of Goods Manufactured (COGM) = $245 million
The ending work in progress inventory roll-forward starts with the beginning balance, adds the manufacturing costs, and then deducts the cost of goods manufactured (COGM).
If we enter those inputs into our WIP formula, we arrive at $25 million as the ending work in progress (WIP), reflecting an increase of $5 million in WIP from the beginning to the end of the period.
- Ending Work in Progress = $20 million + $250 million – $245 million = $25 million
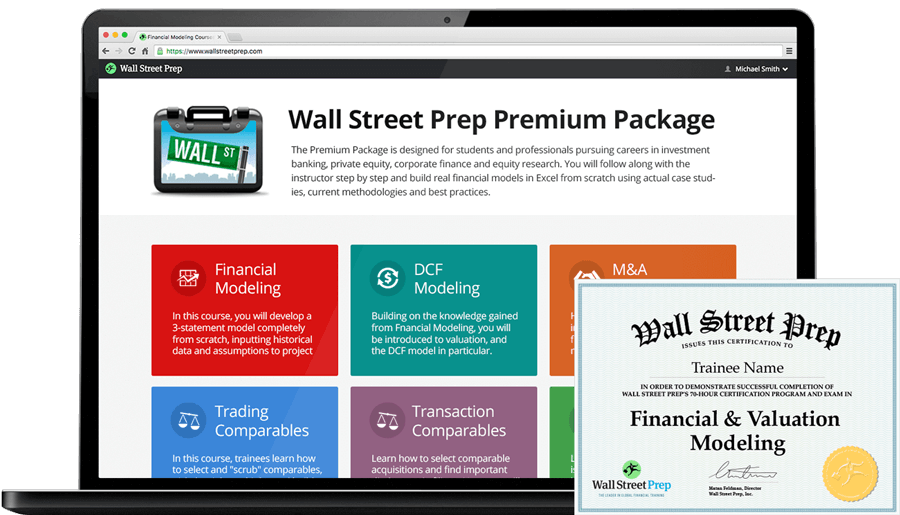
Everything You Need To Master Financial Modeling
Enroll in The Premium Package: Learn Financial Statement Modeling, DCF, M&A, LBO and Comps. The same training program used at top investment banks.
Enroll Today